Lithium Fluoride (LiF) Powder & Pieces Evaporation Materials
Lithium Fluoride (LiF) Powder & Pieces Overview
We sell these pellets and pieces by unit weight for evaporation use in deposition processes. These approximate materials prices are published to provide budgetary guidelines. Actual prices can vary and may be higher or lower, as determined by availability and market fluctuations. To speak to someone directly about current pricing, please click here .
Lithium Fluoride (LiF) General Information
Lithium fluoride is an inorganic compound with a formula of LiF. It has a density of 2.64 g/cc, a melting point of 845°C, and a vapor pressure of 10-4 Torr at 1,180°C. It is crystalline in appearance and white in color. One of its main uses is as a component of molten salts and it is evaporated under vacuum to form anti-reflective layers for optical coatings.
Lithium Fluoride (LiF) Specifications
Material Type | Lithium Fluoride |
Symbol | LiF |
Color/Appearance | White, Crystalline Solid |
Melting Point (°C) | 845 |
Theoretical Density (g/cc) | 2.64 |
Z Ratio | 0.778 |
E-Beam | Good |
Thermal Evaporation Techniques |
Boat: Ni, Ta, Mo, W Crucible: Al2O3 |
E-Beam Crucible Liner Material | Tantalum, Tungsten, Molybdenum |
Temp. (°C) for Given Vap. Press. (Torr) |
10-8: 875 10-6: 1,020 10-4: 1,180 |
UN Number | 3288 |
Comments | Rate control important for optical films. Preheat gently to outgas. |
Empirical Determination of Z-Factor
Unfortunately, Z Factor and Shear Modulus are not readily available for many materials. In this case, the Z-Factor can also be determined empirically using the following method:
- Deposit material until Crystal Life is near 50%, or near the end of life, whichever is sooner.
- Place a new substrate adjacent to the used quartz sensor.
- Set QCM Density to the calibrated value; Tooling to 100%
- Zero thickness
- Deposit approximately 1000 to 5000 A of material on the substrate.
- Use a profilometer or interferometer to measure the actual substrate film thickness.
- Adjust the Z Factor of the instrument until the correct thickness reading is shown.
Another alternative is to change crystals frequently and ignore the error. The graph below shows the % Error in Rate/Thickness from using the wrong Z Factor. For a crystal with 90% life, the error is negligible for even large errors in the programmed versus actual Z Factor.
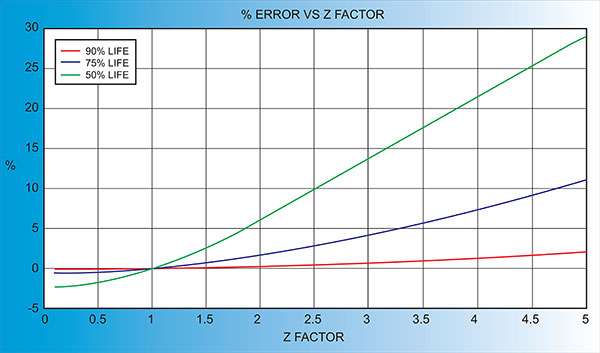
Thermal Evaporation of Lithium Fluoride (LiF)
We recommend performing manual calibration runs on any new material. This allows the user to design a recipe that works for their process. After doing a manual run to start, we have been able to achieve a deposition rate between 1-2 angstroms per second when thermally evaporating lithium fluoride.
Power should be increased slowly in manual mode until a stable rate of 1 angstrom per second is achieved. The run can then be designed around this power set point, becoming the Ramp #2 set point in the recipe. An example of the design would be to set the Ramp #1 power to 65% of Ramp #2 with a ramp time of five minutes. It should be soaked at Ramp #1 for two minutes. After this, go to the Ramp #2 set point and soak for one minute. It is helpful to heat the substrate to 200-300°C.
We recommend evaporating lithium fluoride from a shielded, tantalum crucible heater with an alumina crucible such as our EVCH1 or EVCH10 with EVC9AO if using a KJLC® system. Great care must be taken when installing the heater to prevent the outer shields from becoming warped which can cause a short in the heater, causing the welded joints to fail. The heater should be centered between the contacts and the outer shielding must be clear of the leads. Crucibles should be stored in a cool, dry place and always handled with gloves or forceps.
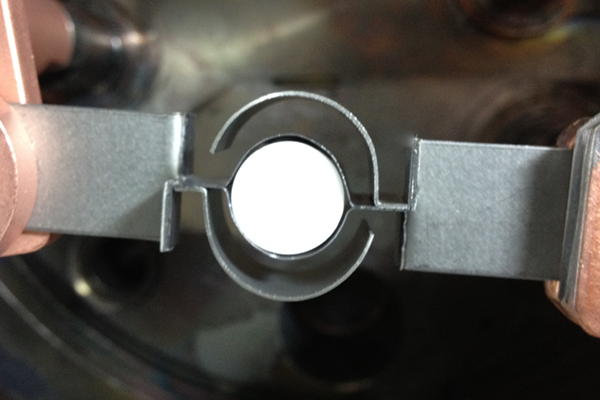
Correct - Crucible heater centered, outer shielding clear of leads
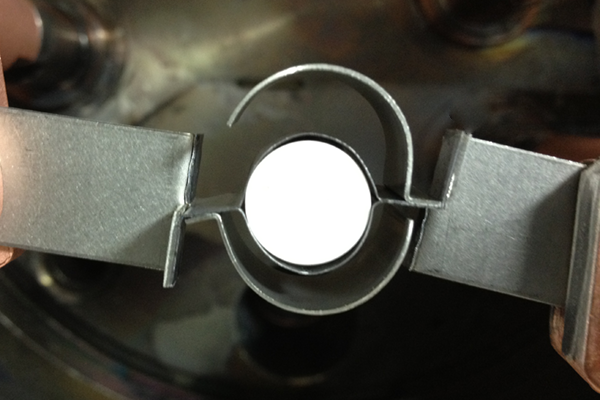
Incorrect - Crucible heater off-center, shielding in contact with leads/inner shielding
E-beam Evaporation of Lithium Fluoride (LiF)
It is important to note that e-beam evaporation of non-metals can be difficult. It generally requires the e-gun to run at a lower voltage. In order to prevent hole drilling of the material, the beam will need to be sufficiently diffused around the center of the pocket. Lithium fluoride is rated 'good' for e-beam evaporation. We recommend using a tantalum, tungsten, or molybdenum crucible liner for evaporation.
Another process note is to consider the fill volume in the e-beam application because we find that the melt level of a material in a crucible directly affects the success of the crucible liner. Overfilling the crucible will cause the material to spill over and create an electrical short between the liner and the hearth. The outcome is cracking in the crucible. This is the most common cause of crucible liner failure. Placing too little material in the crucible or allowing the melt level to get too low can be detrimental to the process as well. When the melt level is below 30%, the e-beam is likely to strike the bottom or walls of the crucible which immediately results in breakage. Our recommendation is to fill the crucible between 2/3 and 3/4 full to prevent these difficulties.
Crucible liners should be stored in a cool, dry place and always handled with gloves or forceps.
See highlighted results that match your result in the table below.
Ordering Table
More Info | Material | Description | Size | Quantity | Purity | Part Number | Price | In Stock | Add To Cart |
---|---|---|---|---|---|---|---|---|---|
More Info | Material | Description | Size | Quantity | Purity | Part Number | Price | In Stock | Add To Cart |
Lithium Fluoride |
LITHIUM FLUORIDE, |
3mm - 6mm Pieces | 100 g | 99.9% | EVMLIFL3-6M | P.O.R. |
|